This summary presents the project Motion Reduction of a Concrete Reduced-draft spar for the Offshore floating Wind iNdustry (CROWN) of the partners Seaplace, USTUTT and sowento GmbH. sowento was in charge of the motion reduction sub-project.
As part of the overall project, Seaplace designed a Floating Offshore Wind Turbine (FOWT) with Reduced Spar Design (RDS) platform for a multi-megawatt turbine. The reduction of turbine motion is achieved by integrating an Anti-Heeling and Ballast System (AHBS), Anti-Roll Tanks (ART) and a turbine controller. In addition, a proof-of-concept of a real-time observer was realised within the framework of CROWN. This is used to reconstruct or observe system states that cannot be measured or that are too complex to measure. In cooperation with the IH Cantabria (IHC), a 1:36 scaled test model was designed and built. This was tested and validated as a HIL system in the wave tank of IHC. The term HIL is used to refer to the test model as a system that is embedded in a control system via its inputs and outputs.
Main results
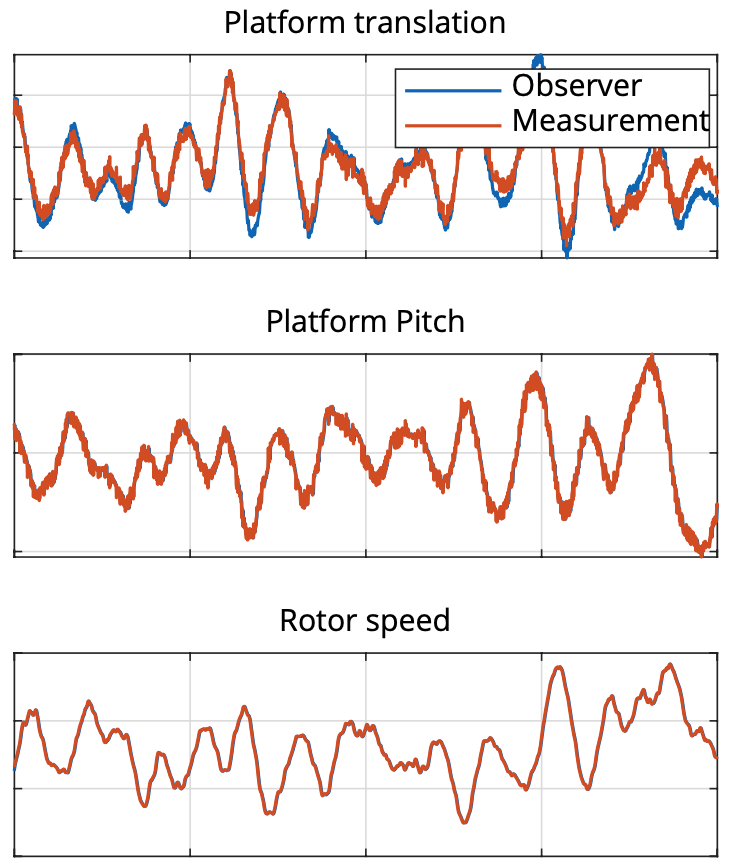
With a focus on the evaluation of the measurements, the most important results for sowento are summarized below:
- Validation of the reduced model SLOW. During the measurement campaign of the scaled FOWT prototype, the SLOW model could be validated. Hereby, the reliability and robustness of the model could be confirmed under consideration of aerodynamics, structural dynamics, hydrodynamics and control.
- Validation of the turbine controller. The controller concept with feedback controller of the RDS plat- form was developed, tested and proven to contribute to the reduction of turbine motion.
- Proof-of-concept of the real-time observer. The measured and observed states showed good agreement. Through the scaled test of the RDS-FOWT, the effective functionality of the real-time observer could be shown. In this context, conducting real tests is a significant step to move from a concept level to an implementation level.
sowento will build on the results to commercialize the digital twin as a platform solution for FOWT load and condition monitoring. It will be combined with a flexible number of sensors, including a nacelle-based lidar for a low-uncertainty reconstruction of the FOWT behavior in every instance of time.
Download the summary report here.